Online Blend Control and Optimizer
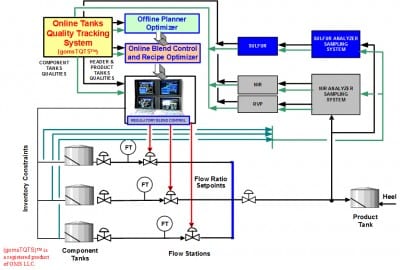
The online blend control is required to adjust the blend recipe in real-time during blend execution to account for changes in blend component qualities, available inventories, blend batch control and any last-minute adjustment in planner’s recipe. It is responsible to deliver the final blend product on spec and on target blend batch size.
Background
In a three-tier architecture of the blending control system, the refinery planner prepares a blend recipe by using gomsPOFBlend™ offline blend optimizer and downloads the blend order to the offsite operations department to execute it online. The objective of blending operations then becomes to make the blend within the planner’s specified constraints yet with latest and sometimes dynamic process conditions. This necessitates the implementation of an online blend control and optimization system (gomsPONBlend™) to produce a blend with a minimum quality giveaway, safely and efficiently.
Applications
Online blending control and optimization scheduling system (gomsPONBlend™) can be used very effectively for:
- Online Execution of planner’s recipe for Gasoline, Diesel and Fuel oil products in a tanks-to-tank blending configuration
- Control the feed quality of the crude unit by blending crude from various sources varying in quality
- Online quality control of run-downs from process units in continuous blending configuration
Benefits
- Minimizes or eliminates the effect of dynamically changing process conditions such as component qualities
- Blends in most economical way by minimizing quality giveaways within planner’s specified constraints
- Online certification for direct blending into pipeline or ship
- Production of economically optimum product blends, thereby adding to refinery’s bottom line profitability
- Eliminates reblends due to violated specs and lack of in-line control
- Flexible configuration of sources and destinations of blends covers all refinery
Figure 1 OMS Online Blend Control and Optimization System
Features
- Blend Setup
- Interfaces with gomsRCPBlend™ or any third party Regulatory Blend control and offline optimizer
- Auto setup of multiple blenders headers dynamically system for product swings
- Initializes the optimizer to check initial data integrity and online control feasibility
- Blend Monitoring
- Automatically collects 250+ pre-configured blend variables for every cycle of execution of tank quality tracking run.
- Monitors online header and stocks analyzers and integrates the latest results in the optimum recipe.
Figure 3 Run-down blenders from process units
Recipe Control & Optimization
gomsPONBlend™ controls the recipe of blend and optimizes every 10 minutes by analyzing the stock qualities and current and target qualities of final product tanks. It archives the LP matrix and solution of every optimizer execution which can be exported to gomsBlendOpt™ system for later analysis and diagnosis.
Interfaces
- Regulatory Control Product Blend System gomsRCPBlend™ or any other third party system
- Offline blend planning, scheduling and optimization system (gomsPOFBlend™)
- Tank gauging system and tanks farm inventory management system gomsTIMS™
- gomsTQTS™ for online tank quality tracking system.
- Blend Information Management System for feedback of model biases (gomsBIMS™)
Recipe Control & Optimization
gomsPONBlend™ controls the recipe of blend and optimizes every 10 minutes by analyzing the stock qualities and current and target qualities of final product tanks. It archives the LP matrix and solution of every optimizer execution which can be exported to gomsBlendOpt™ system for later analysis and diagnosis.
Interfaces
- Regulatory Control Product Blend System gomsRCPBlend™ or any other third party system
- Offline blend planning, scheduling and optimization system (gomsPOFBlend™)
- Tank gauging system and tanks farm inventory management system gomsTIMS™
- gomsTQTS™ for online tank quality tracking system.
- Blend Information Management System for feedback of model biases (gomsBIMS™)
Economics
Economically, it is estimated an annual savings of 5–7MUS$ by online Blend Control and optimization alone. These benefits are achieved cumulatively by integrated three-tier implementation of offline, online and regulator blend control systems.
System Requirements
Intel Core i7 or equivalent, 3+ GHz, 32GB RAM, 1TB+ HDD, CD ROM, 17”+ color monitor, Windows 7 and higher OS
Contact Information
Offsite Management Systems LLC
32003 Baker Estates Dr. Houston, Texas 77094, USA
Tel: +1-832-821-8001 Fax: 866-450-4035
Email: info@globaloms.com Web: www.globaloms.com
Copyright ã 2000-2011 Offsite Management Systems LLC. All rights reserved. OMS™, OMS logo (Tri-circle Triangle), ”…Redefining Excellence”, gomsTIMS™, gomsBlendOpt™, gomsRCPBlend™, gomsTQTS™, gomsPONBlend™, gomsPOFBlend™, gomsBIMS are trademarks of Offsite Management Systems LLC, USA.