Excel Based Single-period, Single-blend Non-linear Offline Blend Optimizer
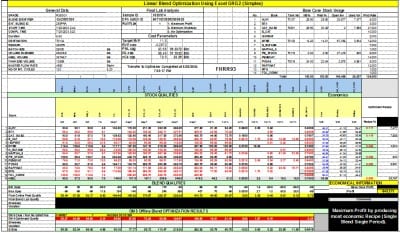
Test
Background
The planning of refinery blend products and the subsequent optimal control of the blending process has a significant immediate impact on refinery profitability and excess inventory. gomsPOFBlend™ off-line blending planning package considers production planning, inventory management, and the quality and value of blending components to optimize blending operations. It is a comprehensive package, which can be modularly integrated in a refinery’s MES structure.
Applications
Offline Product blending optimization, planning and scheduling system (gomsPOFBlend™) can be used very effectively for:
- Single recipe generation for Gasoline, Diesel and Fuel oil products
- Multi-period blend planning for weekly inventory control and monthly production forecast
- Conducting blend studies for operational change modeling and LP verification
- Reblending to correct off-spec blends
- Backcasting to calculate blend models parameters and bias terms
- Analysis of compliance with EPA, CARB rules
- Blend Recipe Management and Automatic downloading of next blends recipes to online execution
Benefits
- Shift usage of more economical components
- Determine and exploit on-the-spot opportunities quickly
- Link refinery-wide planning to short term logistics
- Remove guesswork and artistry from blend planning
- Production of economically optimum product blends, thereby adding to refinery’s bottom line profitability
Figure – 1 OMS Blend Control, Optimization and Planning System Hierarchy
Features
- Basic
- Blending full range of gasoline grades, aviation jet to diesel fuel for distillate blends, and fuel oil blends.
- Multi-period planning with inventory control constraints.
- Number of multiple periods, feed-stock components, and product grades limited only by computer memory size availability.
- Can choose non-linear predictive methods “on the fly” for qualities
- Maximize profit, Minimize quality giveaway, Calculation only optimization Choices
- Determine the header targets for properties for an online system
- Advanced
- Inventory Management – account for changing production and set time dependent limits
- Group Specifications – property constraints over groups of blends
- Heel Tracking – accounting for volume / qualities in tank already, for each use Component
- Pooling – simulate rundowns
- Generalized free-formatted linear and non-linear equations generation and management system (GAMS™)
- User Selectable options for multiple Correlations for 36 qualities
- 3 User definable blend qualities
- Extended
- Octane Blending Values – determine indices for use in LP’s
- Blend Property Control Interfaces- send recipes directly to on-line system
- Biases – add values to correct consistent errors
Figure – 2 Stock Availability Data Entry
-
- Giveaway Ranges – ensure blend remains close to specification
- Infeasibility Control – recover from “impossible” situations, relax constraints until solution is found
- “Distress” Buy / Sell – provides indication of why problem won’t solve, calculate volume / quality needed to make an infeasible problem solve
- Environmental
- EPA RFG Models – blend to emission specifications, ignores extrapolations at iteration-level (may impact), report exactly as written
- CARB Phase II Predictive Model – report emissions, report acceptability
- Modeling and Correlations
- Preferred Recipe Penalties – encourages model to stay near a preferred Starting recipe
- Product Group Limits – volume constraints over groups of blends
- Product Group Relations – relate production of blends to each other
- User selectable built-in well proven correlations for over 40 properties for gasoline, diesel and fuel including EPA RGF and CARB models
- Optimal scheduling of multi-period blends
Interfaces
gomsPOFBlend™ allows direct interface with
- Regulatory and Online blend control and optimization system (gomsPONBlend™)
- Laboratory and Tank gauging data
- gomsTQTS™ for online tank quality tracking system.
- Blend Information Management System for feedback of model biases (gomsBIMS™)
Economics
Economically, it is estimated an annual savings of 750K–1.5MUS$ by Offline Recipe Optimization, and planning and Scheduling of blends.
System Requirements
Intel Core i7 or equivalent, 3+ GHz, 32GB RAM, 1TB+ HDD, CD ROM, 17”+ color monitor, Windows 7 and higher OS
Contact Information
Offsite Management Systems LLC
2003 Baker Estates Dr. Houston, Texas 77094, USA
Tel: +1-832-821-8001 Fax: 866-450-4035
Email: info@globaloms.com Web: www.globaloms.com
Copyright 2000-2015 Offsite Management Systems LLC. All rights reserved. OMS™, OMS logo (Tri-circle Triangle), ”…Redefining Excellence”, gomsTIMS™, gomsTQTS™, gomsPONBlend™, gomsPOFBlend™, gomsBIMS are trademarks of Offsite Management Systems LLC, USA.